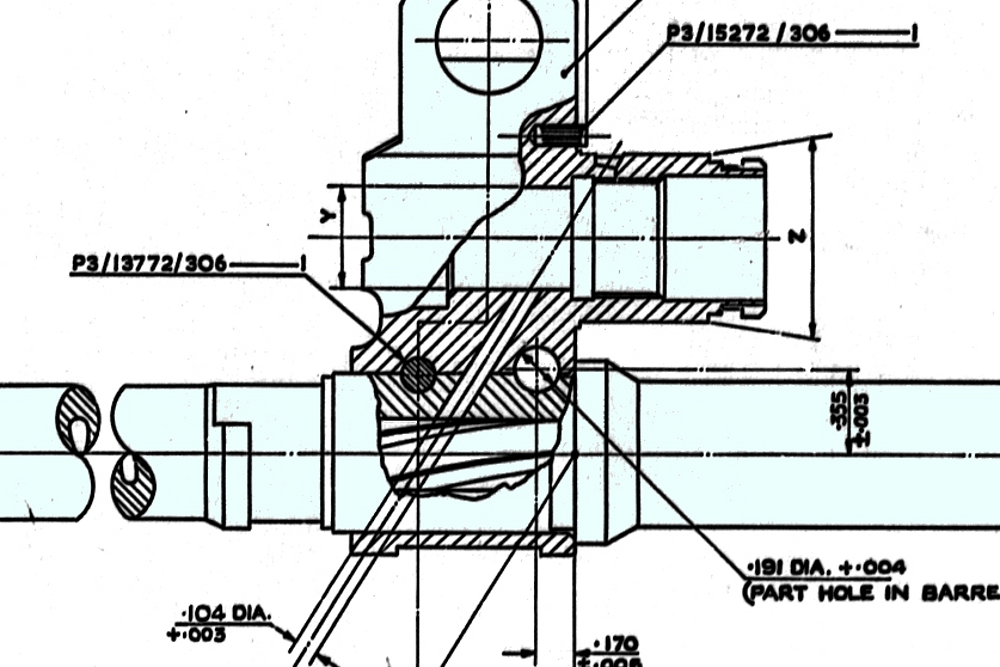
FAL Review: Gas Block Drilling Fixture
is challenging, particularly because there are slight variations that make determining the “correct” location tough.
I used to do it manually – mount a used gasblock in the mill, find the hole center, swap for the virgin gas block, and drill. I came up with a short threaded rod for the front sight hole so I could establish level,
and a nut threaded for the gas cylinder so that the block would always teturn to the same position in my mill vise.
While this was adequate for the relatively rare virgin block, I also had plans to do a run of L1A1 barrels. Many Australian parts kits came in after Republican AG Gonzales “reinterpretted” the Republican’s
import ban to include barrels and recivers (non-sporting), so the barrels had to be chopped.
I had plans to do a run of US made L1A1 barrels and having 150 virgin L1A1 gas blocks to mount, I had to come up with a faster, repeatable method.
I had to come up with something to hold the block perpendicular to use an arbor press for installation.
the original pin is grooved – the best commercial replacement pin I could find that would give a tight interference fit is a M2.5x8mm
and reduce the pin to the exact height. Too long and the regulator won’t contact the gas block and the regulator retaining spring won’t fit.
John Hallis at North Freedom Engineering and we came up with this fixture. He’s a “real” machinist and could take my ideas and put them into practice with a much higher degree of accuracy than I could manage.
Here is what we came up with. The constant dimension on all the gas blocks is the gas chamber hole (except Indian, which is a little tight).
and a threaded 1/2″ OD rod to insure the hole is perpendicular.
I drill the block slightly undersize, mount and pin it to the barrel, and then finish drill it. This is particularly important on the L1A1 which correctly uses a tapered pin.
So I drill to the minor diameter and after mounting, use a #0 tapered drill and then finish with a reamer.
A new L1A1 block will have parallel sight wings, but a used one this may not be so. If in doubt, I use a threaded rod in the front sight hole.
L1A1 barrel should have a horizontal flat at 12:00 on the chamber side, while FAL barrels you can use the vertical wrench flat – after verifying they are parallel.
But the problem I found – testing with many original gas blocks – is the hole locations are close, but not exact. Many (not all) virgin L1A1 blocks have the pin hole location dimpled.
For the first dozen or so, as I refine the locations, it’s a bit annoying. Because I plot one thing (from hole back to zero point) on an existing L1A1 gas block and I get -15.25mm / – 65.53mm.
But then starting at the zero point, I go back to the pre-dimpled point on a virgin block and I get + 15.39 / + 64.78. Then the next one I get + 14.99 / 65.38. So far my max variation is +0.26mm / + 0.75 mm.
Not terrible, but I figure if I log each used and new unit, when I get a dozen data points, I can take the average.
Leave a Reply
You must be logged in to post a comment.