FAL Review: Entréprise Arms Inc. 2007/2008 FAL Receiver
(updated 04-09-2020)
Introduction
I’ve previously had poor experiences with Entréprise Arms. Its not that ALL of their receivers were bad, bat rather they were not consistent one to another. As a professional builder, my customers expect to know before-hand how much a build will cost. While I have built many with no issues, I’ve had significant problems with others. The problems were exasperated by Entréprise’s resistance to deal with problems in an equitable manner. In gunsmithing, time is money. Therefore I had no choice but to refuse to accept any Entréprise receivers for builds.
I was surprised in late August 2007 to receive a call from Entréprise requesting a meeting. I was sceptical, but in late September, I met with Entréprise for the day. They brought several receivers for me to see, described their short and long-term goals, and new management that would correct any past conflicts. They brought several receivers for me to examine and discussed what they had done to improve their products. They left me with two of their newest receivers for me to build and evaluate. It was a pleasant meeting and I left with a belief in their sincerity to build a good reputation on quality products and customer service.
I completed the builds in late November 2007 and have included the following documentary of the builds.
Initial Inspection
I received two Type III (non-lightening cut) receivers for review. Original finish was a dark manganese phosphate “Parkerizing”. The finish was uniform in density and in color. As I had previously refinished the IMBEL parts kits I had selected for the builds, I sand blasted the original finish off the receivers, reapplied a Manganese phosphate coating, and then applied the ARS METACOL IIII Satin Black finish. This accomplished two things. First, it matched the parts kit, and second, as the METACOL III is a smoother finish than Parkerizing, it highlights surface detail to assist in my photography.
Receiver serial numbers were IM 2353 and IM 2354. Overall appearance was good.
The front outside compound radius is probably the most difficult machining operation
Receiver markings were “TYPE 03 METRIC 7.62MM” on the left side and “ENTREPRISE ARMS – IRWINDALE CA USA” on the right side. Serial number placement is under the ejection port. Lettering was deeper on one receiver than the other. I expressed my personal preference for smaller, discrete markings and that this may also be preferred by other builders. BATFE marking requirements are minimum 1/16″ high and 0.003″ deep.
Ejector Block, Magazine Fit, Feed Ramps
Ejector blocks are traditionally installed in a receiver, and the the receiver and the ejector block are drilled together for the two retaining pins. Using surplus ejector blocks does not always guarantee the holes will line up. Additionally, the corners of the surplus ejector blocks don’t always have the same radius as the new receiver. Also, surplus ejector blocks are cut for the full-auto sear. It is not illegal to use a full-auto ejector block in a semiauto receiver. The semiauto receiver would have to be machined to accept the auto sear. It is this step that is (for non-licensed people) a violation of the National Firearms act.
Traditionally, the full auto slot in the ejector block is blocked off by weld. The ejector block establishes the front to rear distance of the magazine well, and also the relationship of the magazine catch to the back of the magazine. Previously, Entréprise has used surplus ejector blocks and tried to work around all the additional difficulties this entails. On this version of the receiver, Entréprise manufactured their own ejector blocks to obtain consistent fit with their receivers. I think this is a good idea. The fit of the ejector blocks is tight on both the sides and the rear, and the two retaining pins are machined flush to the receiver and are barely visible. The ejector is integral to the block (some FAL variants have the ejector as a separate piece).
One problem I discovered was a small shoulder of metal on the receiver under the ejector block where the magazine catch inserts. This lip would snag the magazine catch and prevent it from engaging completely. I used a cut-off wheel on my rotary tool to grind this small shoulder flush.
The front magazine notch was clean. Magazines installed without issue.
Feed ramps were slightly uneven and the center peak varied slightly in contour from one receiver to the other, but had no effect on feeding. A rotary tool with a pencil handle and 1/4″ fine sanding drum will work well to polish these surfaces, if desired.
Barrel Timing and Headspace
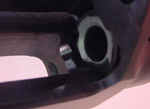
Another important dimension is the receiver face relative to the indexing of the barrel threads. It is critical that the threads start at exactly the same point on every receiver. Ideally, the barrel will hand-tighten to approximately 10:30 on a clock face. This equates to 15 degrees short. When subjected to torque of approximately 120 ft pounds, the barrel should draw to top dead center. The red triangles represent the ideal spot for a barrel to hand-time.
I tried 3 different IMBEL barrels on each receiver. All timed short. If there is going to be a variance, it is better for the variance to be short than long. If short, one can simply remove a few thousandths of an inch from the barrel shoulder. If it over-times, then one must turn the shoulder back enough to accept a spacing (breeching) washer as used on the Commonwealth L1A1 rifles. The rear handguard support and the rear gas tube support will then have to trimmed to clear the breeching washer (or use an inch pattern).
While the timing was a little short, I don’t consider it a major issue. Also, the chamber face contacted the inside of the receiver before the barrel timed to top dead center. The solution is to trim the chamber face back a few thousandths of an inch. I just turned it a few times against a belt-sander and then a 3M Scotchbrite polishing wheel. This same phenomenon occurs frequently on IMBEL factory receivers, so I consider it just another step in the build and not a defect.
After installing the barrels, I set the headspace. One receiver required a 0.264″ locking shoulder, which is typical. The other receiver required a 0.268″ locking shoulder, which is uncommon on the large size. It is possible the barrel I used had a chamber that was slightly longer than typical. On a headspace too tight (and non-chrome lined barrel) I can ream the chamber deeper to use a locking shoulder in the more common range of 0.256″ to 0.264″, or file the locking shoulder to fit. Requiring sizes above 0.264″ can be problematic, as they simply aren’t commonly available. Fortunately, I had a few locking shoulders in the less-common 0.265″ to 0.270″ range.
Upper to Lower Receiver Lockup
The rear locking ledge is a critical dimension. It controls the up and down movement of the lower receiver when closed. The locking body is tapered to match the 10 degree angle of the ledge. This wedge fit maintains tightness even if one surface or the other should wear. Entreprise has the correct angle, however both lowers were slightly loose. One barely moved, while the other had slightly more movement. I corrected the fit by welding up the locking body and recutting it slightly oversize. It is a possible that both the lower receivers I selected were off. I’d need a larger statistical sampling to be sure. I tried several different locking bodies before deciding to add a bead of weld to the locking body engagement surface to obtain a tighter fit. I conclude that the locking ledges are low by approximately 0.026″ (original locking body height at rear of wedge 0.358″, after welding 0.384″). This is a small, but critical amount. If there has to be an error, I think it is better to be slightly oversize, as it is far easier to take a few strokes with a file on the locking body than to weld it up. Furthermore, if slightly oversize, the wedge relationship between the two surfaces will still keep the lower tightly locked to the upper (too large and the lower will pop open under recoil). There are oversize locking bodies but these are rare.
This is the only problem I had with the two builds that was not easily correctable. It added about 15 minutes to the build time to TIG weld the two locking bodies, and another 15 minutes to regrind the correct angles. Although welding the locking body is safer, as an inexpensive part to ruin, if I hadn’t already refinished the receivers, I probably would have welded up the locking lug instead of the locking body. Rebuilding the locking lug is a normal procedure for arsenal rebuilds of military rifles. Having the proper tooling to regrind the correct 10 degree angle is probably beyond the resources of most home builders.
Final Assembly and Testing
The gas piston was correctly flush with the inside of the receiver.
I installed new Belgium dust-covers and then discovered the bolt carrier wouldn’t close all the way; they stopped about 1/4″ short of battery. I removed the dust cover and the bolt carriers slid right in. I discovered the receiver clearance cut for the dustcover was slightly uneven and a little undersize. I used a small cutter on my rotary tool to open this radius and prevent the dustcover from pinching the top leading edge of the bolt carrier.
I function tested and zeroed both rifles with 30 rounds each of delinked Malaysian ammunition. Both rifles functioned and zeroed without any trouble.
Summary
The two receivers I tested are the newest offering from Entréprise Arms. I experienced the following issues during the build
- Barrels timed short – I turned the barrel shoulders back slightly.
- Chamber face bottomed out on inside of receiver – Common even on factory IMBELs, I shaved the face slightly
- One rifle required a larger than common locking shoulder – possibly a barrel chamber issue.
- Magazine catch caught on small ledge – I removed the ledge.
- Dust cover pinched the top of the bolt carrier – I slightly relieved the dust-cover clearance cut.
- Slightly loose lockup between upper and lower receiver – I welded up the locking body and recut it oversize.
Only the final issue was of any consequence. Even with these minor issues, I am pleased that the issues were identical on both receivers. Consistency is important. Knowing before-hand what minor adjustments may need to be made make for a smooth build. I expect Entrérprise will examine the issues I have identified. Based on these two receivers, I have no objection to accepting this latest generation of Entréprise receivers for build. With the Federal ban on importing FAL receivers, I am pleased to see there is another viable choice in the domestic FAL receiver market.
Leave a Reply
You must be logged in to post a comment.