Introduction
There are several companies that have operated under the name “Williams Arms” or variations. Dwight Williams of Williams Arms Company, in Sisters, Oregon, introduced the Aluminum Combat Elite around August 2001. It did not fare well in real-world and laboratory testing. Several gunsmiths have had success in building these aluminium receivers into .223 Rem and .45 ACP rifles. See my Williams Arms Company Aluminum Receiver review
The purpose of this review is to evaluate the steel receiver for dimensional and cosmetic congruence, or variations from, a “standard” set by Fabrique Nationale Herstal as exemplified by Belgium made or Belgium licensed (Brazilian IMBEL) receivers.
US Armament selected me to provide an objective review. While I doubt I will be nominated for “Diplomat of the Year” my credibility as an objective evaluator is of utmost importance to me and I think WAC knows they will get a fair and thorough review. Clearly stipulated in our agreement is that the receiver is free with no obligations other than to provide an objective review in a timely manner. I regret that it has taken me a few weeks longer to complete the review than initially anticipated. My shop has built over 3000 rifles on a dozen receiver types and I consider myself competent to evaluate variations from standard, with “standard” being a Belgium FN receiver or a Brazilian IMBEL receiver. I am not qualified to assess the metal type or its long-term durability.
On 21 August 2002, I posted the initial photographic review of the bare receiver. The questions raised from the initial photographs will be answered below. On 08 September 2002, I finished assembling the rifle and I successfully testfired the rifle on 09 September 2002.
Review
Overall finish is excellent. Machine marks are present, but far less prominent than a typical FN licensed receiver. Edges are crisp. I cannot tell if the receiver is machined from a billet, a forged billet, a casting, or a forging. The configuration is unusual: it is closest to the T48 style rifle, a modification of the FAL Canada used for the US Army testing and the German Police testing. It incorporates relief cuts for the tabs on an inch pattern or stripper-clip guide dustcover, which is not found on a typical metric. Receiver has both sets of internal lightening scallops, as well as the rail cut which serves as a place for debris to accumulate rather than obstructing the action.
The terms “sand cuts” and “lightening cuts” are mostly interchangeable in describing these features. The external lightening cuts are similar to a metric, however with a slightly different contour and radius. The inside center of the receiver has a hole which I have not seen on any licensed FN receiver. I suspect that it is an aid for fixturing the receiver in the milling machine.
The clearance around the gas piston hole (a), the dustcover radius (b) and the feedramp scallops (c) are the only spots that suggests the receiver started as a casting. The gas piston hole is in the correct location and its surrounding recess is properly centered. The radius for the dustcover is correct. The notch for the front of the magazine (d) is deeper and wider than a typical metric receiver. It is not wide or deep enough to accept inch-pattern magazines. The critical dimension of this cut is the bottom shelf (e) and it is correct for holding the magazine at the proper height. I consider this unusual cut to be “different” but not “wrong” as it works for its designed function.
These pictures show a close-up of the relief cuts (f) for the tabs on an inch-pattern or stripper-clip guide dustcover. It also shows a relief cut (g) that assists in installing the dustcover, however it is on both sides, while a typical metric is on the right side only. It also shows the nicely done internal lightening/sand cuts (h), the unusual hole in the receiver (i) and the locking ledge (j) which is of the correct height and angle. Bottom picture shows the correct, barely noticeable “swelling” of the underside receiver walls, which engage the faint cutout on top edges of the trigger housing. The bracketed area shows a small cosmetic flaw an end mill gouged slightly – maybe a broken flute or a metal chip that didn’t rinse clear with the coolant.
These pictures show a close-up of the locking shoulder dog leg recess (k) which is properly located over the locking shoulder hole and the correct dimension. The correct lightening cut (l) is behind the hinge pin hole.The magazine well lightening cut (m) is a 90 degree angle, instead of the radius cut of an FN receiver. The front set of lightening/sand cuts (n) are present and in the correct location, and the subtle reduction in rail height cut (o) is also present and correct for a type I metric.
The locking shoulder hole (p) is even. The groove for the dustcover is incorrect for a metric receiver at position (q). This cut goes all the way through to the ejection port. On a standard metric, it stops short of the ejection port. In practical terms, this will have no effect unless used with a stripper-clip dustcover without the tabs. Such a dustcover would slide forward under recoil and obstruct the ejection port. In fairness, since this receiver incorporates the recess cuts for the the tabs of an unmodified stripper-clip cover, There would be no reason to remove the tabs as is often done to use such a dustcover on a standard metric receiver. The ejector block fits well with no significant gap between the ejector block and the receiver.
This picture shows the unique “bottom dead center” (BDC) mark, which may assist some in barrel alignment. Its too bad all receivers and barrels don’t have this mark – on many, its stamped between the barrel and receiver, but not in any particular orientation – just a witness mark for reinstalling the barrel to the same spot. Notice also the correct interrupt in the threads for the barrel, and the nicely machined receiver face.
These pictures show an area over which I initially had great concern. The extractor relief cut on the left is the Williams Arms receiver. Notice it is a sharp 90 degree shoulder. The IMBEL pictured is a gradual contour. I resisted the urge to “fix it” because if it was a defect, I needed to let it fail and document it. I was pleasantly surprised to find no effect. Perhaps it is an improvement. Since it is a clearance cut, it is the minimum, not maximum dimension that is important so I will consider this as another “different” but not “wrong” attribute.
These two pictures show timing with a used Brazilian barrel and a new Argentine Barrel). Both hand tightened a little bit short compared to an IMBEL receiver, however after turning the shoulders for a 15 degree short of TDC timing, neither chamber face contacted the inside of the receiver, which is good. Even some IMBEL receivers will contact on the chamber face. On a Mauser, this is the secondary torque shoulder, however on a FAL it is not supposed to contact. Some professionals speculate that a gap improves accuracy however I have been unable to quantify this hypothesis.
These three pictures show my greatest complaint with this receiver – the engraving is neither deep enough, nor crisp enough. Definitely not deep enough to hold paint. It looks like it was acid etched, although it was probably engraved with a too-wide ball endmill. The edges just don’t have the crispness that is possible with a good CNC writing program. While this is not a structural flaw, I think making the lettering smaller, deeper, and sharper will dramatically improve the aesthetics of the receiver.
I selected a DansSports “Grade II” Brazilian barrel and promptly over-timed the shoulder so it would hand tighten to TDC. Rather than try to fix that barrel and possibly compromise the integrity of my evaluation, I selected another “Grade II” Brazilian non-bipod cut barrel from DansSports and shortened and rethread to 18″ with a .116″ gas port. Even after shortening, there was still faint etching/pitting in the chrome-lined bore. I selected a First Son Enterprises fake Belgium short flash suppressor and soldered it on with “Fusion” brand 1100 degree solder per ATF specifications (The Federal requirement for permanently attaching a muzzlebrake expired in September of 2004, although some states have retained it). After turning the shoulder for a hand-tight 15 degree short of TDC, I cranked it on with a custom receiver wrench to a “feel” torque pressure between 100 and 125 foot pounds.
I selected a G1 bolt and carrier assembly and a G1 .261″ locking shoulder, which did not close with double thumb pressure on a Forster Brand NO GO gauge, but closed easy on a GO gauge. I finished the assembly with a First Son Enterprises Hammer, Trigger and Sear after increasing slightly the forward rake on the sear nose. I did this because for testing purposes, I preferred a slightly heavier trigger with very tight engagement – eliminating variables. I then selected a new Austrian pistol grip from DSA, a Belgium gas piston measuring .4295″, a Penguin Small Arms Works humpback stock and non-bipod cut handguards. I used a new DSA cocking handle and plastic knob and left the carry handle off (its not a bloody purse) with a DSA handguard spacer
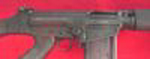
I live in Arizona, and this build was during the peak of summer heat. Temperatures at my outdoor 100+ meter shooting spot reach an uncomfortable 120 degrees F. in early afternoon. So I opted to test it at a local indoor 25 meter air-condition range. I used Belgium aluminum magazines with a random mix of approximately equal quantities of L2A1 Radway Green, Malaysian, and Portuguese ammunition. The Malaysian was delinked from machinegun belts and had some mild discoloration. Having read some silly “torture tests” where people fired the guns until the barrels glowed red, I opted for a little bit more realistic testing. I performed aimed fire at a 1″ target at 25 meters from kneeling supported position. Approximate rate of fire was 20 rounds per minute, or one round methodically every two seconds with a 10 second magazine change. I fired 5 rounds to zero (timing was right on), five rounds to confirm my zero, then a 20 round group. I made another slight windage adjustment, changed targets and fired a 260 round group. At 260 rounds, the handguards got too hot to hold, so I switched to a “rice paddy prone” squatting position holding the rifle by the front of the magazine. I fired an additional 120 rounds for a total of 410 rounds. At this point, the range was closing and I didn’t have time to go out to my truck for another 200 round can. I think the 400 rounds was sufficient. I experienced zero malfunctions. Returning to the shop, I rechecked the headspace, and it had increased by less than .001″ which is normal for “setback” and mating of components after initial firing.
I experienced one minor problem during assembly. The recess for the head of the magazine catch screw was offset from the hole for the shaft by a very small amount – just enough that it made tightening the screw difficult. I turned approximately .001″ off the head of the screw on a 3M Scotchbrite deburring wheel and it screwed in just fine. I manually cycled 10 USGI dummy rounds through the gun with one incomplete chambering which I blamed on the fact that these dummy rounds were pretty beat up from daily use. At this point I was reasonably confident it would run, so stripped it and sandblasted the parts with #80 aluminum oxide, and finished it in dark gray manganese phosphate. Reassembly confirmed the lettering was simply not deep enough to attractively fill with white paint.
The receiver went together easily with no significant issues. Rifle testfired fine. With the caveat that I am not qualified for an in-depth metallurgical analysis, and cannot predict long term serviceability, my initial testing was satisfactory and I have no reservations building customer supplied guns on these receivers
Summary
The Williams Arms “HC Elite” Steel FAL receiver supplied for this review assembled normally and survived a 400 round testfire with no problems. Assuming the unit I received is a representative sample, I have no reservations on building rifles on this receiver.
Dwight Williams of WAC (Sisters Oregon) “sold” his business to U.S. Armament Company, where Dwight now works. The ownership of the Williams Arms Company cum U.S. Armament is in question, with Dwight Williams being the registrant of U.S. Armament as a web entity. U.S. Armament has made public “good faith” announcements to compensate purchasers of the aluminum receivers by offering a steel receiver, with credit given for the return of the aluminum receiver. To the best of my knowledge, WAC has never honored their agreement, and the only steel receivers made are the few distributed to gunsmiths like myself for review.
Leave a Reply
You must be logged in to post a comment.