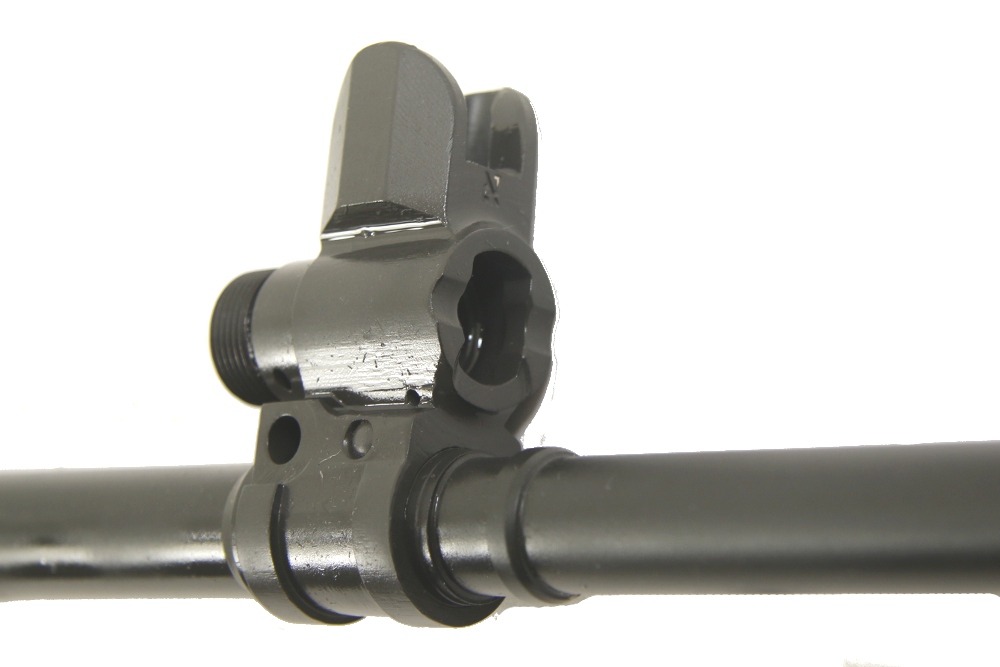
FAL Tutorial: Installing FAL Israel Gas Block
Thanks to the Republican ban on importing “non-sporting” barrels, the recent influx of Israeli ROMAT parts kits came with the barrels cut. DS Arms had some barrels made. The first batch were defective, which they knew, but they sold them anyway (it’s The Chicago Way!). The gas block journals were undersize, such that a gas block would spin freely. To add insult to injury, DSA’s representative on FALFiles came up with some bullshit story about how removing the gas block from the old barrel section “stretched it”. (((sigh)))
I’ll get to salvaging one of these undersize barrels later. For now, we’re going to look at installation procedure on the second run of barrels which are much better.
Remove gas block from barrel section by driving out the gasblock retaining pin. Then set the rear portion of the barrel section in a vise with just enough tension to hold it. Drive the barrel section to the rear.
Test fit the gas block to the journal. If it spins with no effort. Stop. You will need to return the defective barrel or build up the journal with solder (covered later).
Apply a thin oil to the barrel journal. If the block ios too tight, a light sanding with fine emory should be sufficient. The goal is to have it tight enough that some effort is needed to move it rotationally.
I use tapping fluid because of its anti-galling properties.
Drive the block on using a tube with a brass or aluminum fitting. Strikling the block with a steel hammer will deform it. Depending on tightness, you may be able to use a wood block. I use an aircraft riveting tool with a black iron pipe and brass fitting.
Use a level on the flat to orient the barrel vertically. On an Israeli gas block, you can use a level on the front sight flat.
On standard FAL and L1A1 gas blocks, you will need a threaded rod in the front sight hole to verify vertical alignment.
Orienting the block 90 degrees from vertical, use a 1/8″ end mill to start the hole. A drill bit contacting the round barrel section will want to climb, following the contour. It is important to start with a flat spot. One can also use a carbide chisel point drill to start the hole. I do the same from either side, so that any error is reduced by half.
Drill the gas block retaining pin hole larger – half way from either side – with a 9/64″ Then through drill #24 (.152″). This should make for a good interference fit for a 5/32″ (.156″) pin.
Use the same technique with a #9 and a 13/64″ bit for the screw hole. Be sure to install the pin first.
Drill gas port to .098″. Having done dozens of these, almost all are a little sluggish at .098″ so I drill to .106″.
Leave a Reply
You must be logged in to post a comment.