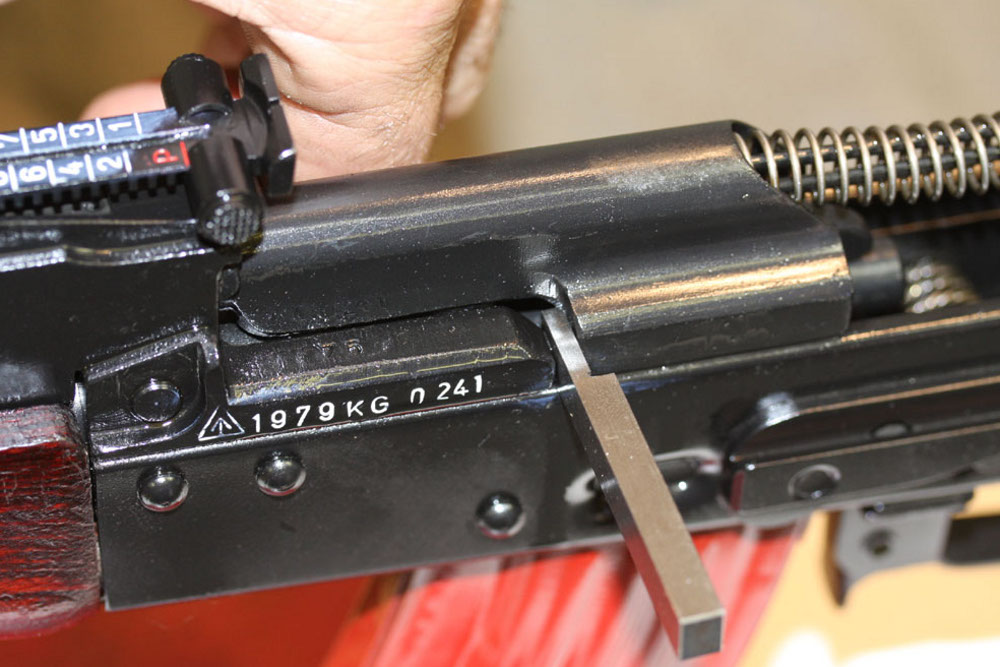
Tool Review: East German AK Armorer Tools
The East Germans produced a nice armorer tool chest for the AKM (MPi-KM/KMS-72), RPK (MPi-LMG) and the Makarov (Pistole – M). With the help of John Baum at GermanManuals.com , I have figured out what they all are for. Here are the ones for the AK family. The numbers are the East German part numbers. V seems to associate to a fixture, while W seems to correspond to a tool, and L to a gauge.
I’m not one of those who must have everything original, to fondle under candle-light . . . while naked. They are just tools to me.
this holds the firing pin flat to the rear of the bolt, to allow the firing pin to be measured with a protrusion gauge.
The vertical hole is for the firing pin retaining pin, the diagonal hole is for the extractor retaining pin.
I rarely need it, but on the rare instance where a firing pin retaining pin is stuck, this is very helpful.
I made a sleeve for 5.45mm bolts.
I’ve used this frequently, on guns where the catch lever was flopping around. It’s important to support the rear sight base – not because the base will compress, but because the end of the catch is thin. Failure to support the overall length of the catch axle will result in the end of the catch bending, rather than the outside area flaring (ask me how I know).
This keeps force on the axle and off the rear sight base.
given that new top covers, are relatively inexpensive, I’ve not found a need to actually repair a dented cover.
a selector that bypasses the stop n the top cover, will push the disconnector forward and with it, causing the trigger to rotate back – firing the rifle.
Since American shooters often want to switch their furniture around, I do not stake this bolt on customer guns. Once staked, this bolt becomes a threaded rivet.
I’ve not used it for its intended purpose, as gas tubes are usually cheaper to replace than to repair. I have used it to secure a gas tube in the mill vise, for recutting the cam angle for the retaining lever, after building up a loose one with weld.
this is a tough one. I can usually remove an upper handguard by clamping the gas tube in a vise, on the receiver side, and then pressing down hard with my hand and rotating. Or by holding the handguard and using an open-end wrench. But there are times when the handguard is on so tight I must use this tool. The problem is, if it is tight enough to need the tool, using the tool will often mar the handguard. So it’s a last resort.
I don’t see many customer guns that use a nut instead of the slant brake, and the nut is so tight that the wrench is useful. If it is seized, vibrating the heck out of it with an air-hammer and a nylon tip, will usually work it loose.
This is another of the last-resort tools. If the nut is so tight, and vibrating with a nylon-tipped air hammer is insufficient, then it’s also probably too tight to keep this tool engaged. The ramp portion of the slant brake makes the tool want to climb off. Where I do like it is when I have threads that are just tight – it allows me to work the brake back and forth and lap out any high spots.
At the time of this writing, quality steel magazines are $15. So there is a limit to how much time I can spend “repairing” a magazine, before it exceeds replacement cost. But there have occasions for it. The shortcoming is that it only helps for dents in the flats, not the ribs. For those I use shaped grade 5 bolts and a hammer – see the section on FAL magazine repair.
I’ve found that for most magazine axles, the point on this punch and mandrel are too sharp – they bottom out while the flaring is still incomplete. So I rounded off the tips and they now work much better. Magazine catch height, particularly in 5.45 and 5.56 AKs, is a significant cause of feeding problems, so I use this tool all the time.
These are the single greatest prize in the chest. The job is so much harder without it. Assemble the mag catch and spring using a 4mm punch as a slave. Once squeezed, the slave can be removed, the assembly inserted in the trigger guard, and the catch axle inserted. Easier with three hands, but I’ve managed it by myself hundreds of times.
Filing a little step in it makes it work better for the flat bottom AK74 mag catch.
when welding up an undersize mag catch, this is a quick and easy way to confirm the angle. Since the sides of the catch can be crushed if tightened in a mill vise, I typically reshape on a belt sander. Having this in one hand keeps my angle correct.
New magazine catches come with the stop oversize. It must be filed to obtain the dimensions G and A. I’ve had enough practice that I can eye-ball it, but it’s nice to be able to confirm with the gauge.
The chest came with 2 of these and I’ve broken one already. The US commercial one that is closed on the sides, tends to work better.
broke them on first use. Could be a fluke, but the modified screwdriver shown in the ARS tools section, works very well.
Filing a little step in it makes it work better for the flat bottom AK74 mag catch
this has little application for the gunsmith. For a unit armorer, it allows a record of front sight height, so that it can be returned to that height after repair work. Presumably, this makes re-zeroing faster.
This is very useful for installing a new threaded cylinder. For actual windage adjustment, I prefer the large Chinese unit, as it will work also on unitized gas block sights (like on the AK74u), and this unit will not.
It is traditional after a rifle is zeroed, to stake an index mark on the cylinder, crossing the front sight base.
I really like this simple tool and use it all the time. The push function is particularly useful, as the pull function can be duplicated with any hook.
Generally speaking, 1/8 turn of the gas piston establishes the proper overall length, but this is a convenient (albeit complicated) method for confirming.
an original stock screw is concave and designed to be fared, converting it to a flared rivet. I will counterbore commercial screws for the same purpose. Loctite is generally insufficient. The heavy vibrations of an AK firing, tend to make any screw want to walk out.
Leave it to the Germans! This is actually a great tool, unfortunately the East German screw is different than Russian or Romanian, so it’s of limited use. But it sure is nice not to fight initial screw installation in in a virgin stock.
After years of use, I broke this end, but using a carbide cutter, I was able to fabricate a new slot.
Leave a Reply
You must be logged in to post a comment.